PUBLICADO EN POR ADMIN
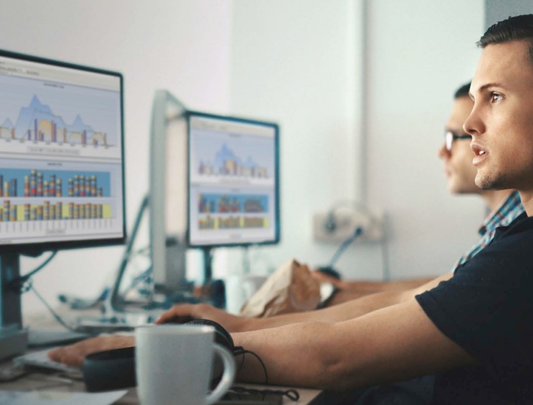
Contenido
¿POR QUÉ USAR SOLUCIONES DE PLANIFICACIÓN DE LA PRODUCCIÓN?
¿QUE OBTIENEN LAS EMPRESAS QUE USAN APS?
En la actualidad, es prácticamente inconcebible imaginar que un gran porcentaje de medianas grandes empresas dedicadas a la fabricación en EE.UU. sigan planificando sus fábricas de forma manual, mediante hojas de cálculo (Fuente: The Little Blue Book on Scheduling, de Mike Liddell). Y, sin embargo, creemos que es así.
Teniendo esto en cuenta, resulta importante recordar que existen numerosas historias de grandes éxitos de fabricantes que han sido capaces de implementar soluciones de planificación y programación avanzadas (APS) de manera favorable.
Según nuestros cálculos, solo un pequeño porcentaje de medianos y grandes fabricantes de EE. UU. han sido capaces de automatizar sus procesos de programación. Estas empresas están alcanzando enormes beneficios día tras día, mes tras mes y año tras año, simplemente porque ahora pueden programar sus fábricas de forma inteligente en poco tiempo, lo que antes se requería hacerlo de forma manual.
Que obtienen las empresas que usan un sistema APS?
Normalmente, estas empresas mejoran la puntualidad de las entregas, aumentan la productividad y eliminan gran parte de la confusión que causan los cambios y la programación manuales. En resumen, estas empresas disponen de una ventaja estratégica con respecto a su competencia simplemente porque son capaces de reaccionar de forma más ágil e inteligente ante los cambios. Y esto es todavía más relevante ahora que se acerca la industria 4.0.
Para obtener una idea más clara del problema, resulta útil volver la vista atrás, a la década de los 80, cuando los fabricantes empezaban a usar el software de planificación de requisitos de material (MRP). Dado que el MRP facilitaba a los fabricantes la gestión de las restricciones de material, estos comenzaron a idear formas de resolver sus problemas más importantes, causados por las restricciones de capacidad.
Cuando los proveedores de software comenzaron a presentar soluciones de planificación de recursos empresariales (ERP), a simple vista estas parecían ofrecer lo que todos andaban buscando. Resultó que los sistemas de ERP hicieron un trabajo formidable integrando los datos en las áreas funcionales y gestionando el aspecto transaccional de las empresas de fabricación; sin embargo, no les ayudaron a gestionar sus recursos de fabricación.
Metodología de trabajo
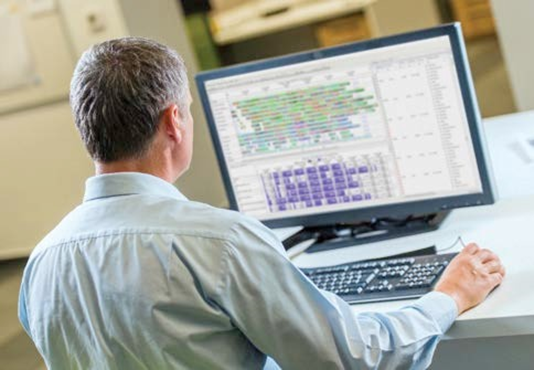
Dado que la mayoría de los programadores trabajaban cómodamente con Microsoft® Excel, las hojas de cálculo se convirtieron durante 20 o 30 años en el principal mecanismo utilizado por la mayoría de empresas para crear programas de planificación de la producción.
No es complicado crear un programa con Excel, pero actualizarlo y calcular el impacto descendente cuando se efectúan cambios resulta increíblemente pesado y lento. Debido a los conocimientos y las habilidades necesarios para crear un programa manual, los programadores pasaron a ser personas indispensables, y muchas empresas empezaron a darse cuenta de lo vulnerables que eran cuando perdían a alguno de ellos.
El problema fue que la creación de un software que diseñara programas precisos y realistas, basados en las limitaciones del mundo real, resultó ser mucho más complicado de lo que nadie hubiera augurado, incluido el propio Goldratt.
Soluciones APS
En un comienzo, los desarrolladores de software comenzaron creando lo que ellos denominaban “soluciones de programación de capacidad finita” (FCS, por sus siglas en inglés). Con el paso del tiempo, las soluciones de FCS se ampliaron e incluyeron la gestión de planificaciones y de otras limitaciones, y en la actualidad se las conoce como “soluciones de planificación y programación avanzadas” (APS, por sus siglas en inglés).
Las empresas de software invirtieron millones en el desarrollo de soluciones de APS de alto rendimiento, ya que proclamaban que estas optimizarían la forma en que las fábricas se programaban; sin embargo, la mayor parte de estos sistemas fracasaron estrepitosamente en el mundo real.
La única razón del fracaso de estos sistemas fue su incapacidad de producir programas precisos que incorporaran el conocimiento tradicional, esencial para gestionar la mayoría de fábricas. Y, lo que es más importante, no existía ningún mecanismo que permitiera modificar la forma en la que los programas se creaban para incluir este tipo de conocimiento.
Si el programa no tenía sentido, nadie lo adoptaba, y si nadie lo usaba, se convertía en una tarea inútil.
Opcenter APS (Anteriormente llamado Preactor)
La buena noticia es que, en la actualidad, sabemos cómo crear programas que incluyan (reglas) heurísticas que incluyan tanto los datos esenciales como el conocimiento tradicional.
Además, existe una fórmula sencilla que garantiza la implementación exitosa de un sistema APS. De hecho, solo debe disponer de tres elementos:
- El software de APS adecuado
- El proveedor de implementación adecuado
- Los recursos internos adecuados
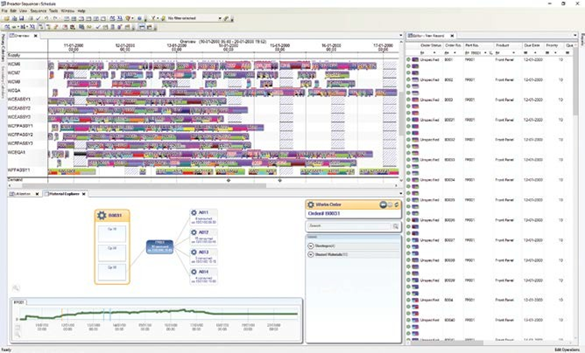
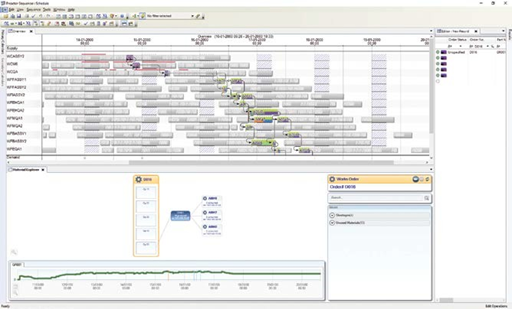
Las consecuencias de prescindir de alguno de ellos serán elevadas y afectarán considerablemente a sus probabilidades de éxito si alguna vez decide volver a intentarlo.
Si no elige el software adecuado, en algún momento deberá echar por tierra todo el camino recorrido y comenzar de nuevo. A su vez, si no encuentra el proveedor de implementación adecuado, podría tardar dos o tres veces más en llegar a la meta que se ha fijado (si es que consigue alcanzarla). Dado que el éxito trae consigo importantes recompensas y que el fracaso tiene un alto precio, no tiene sentido buscar la solución más barata
Las soluciones de OPCENTER APS ayudan a los fabricantes a mejorar la sincronización de sus procesos de fabricación otorgándoles una gran visibilidad y control para aumentar la utilización y la puntualidad de las entregas, a la vez que reducen los niveles de inventario y las pérdidas.
Beneficios de usar Opcenter APS
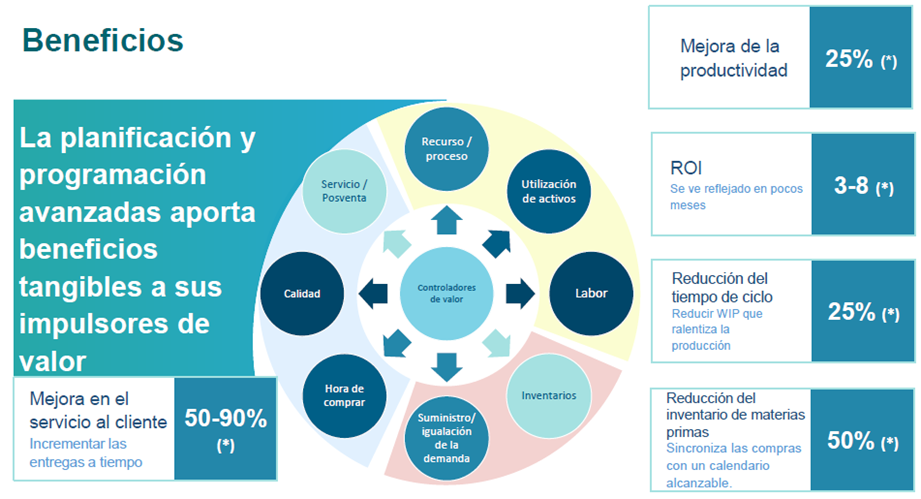